採購和倉儲活動的重組和優化
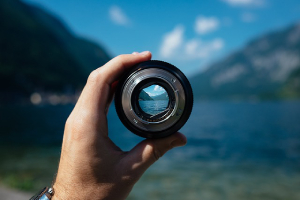
Manager:
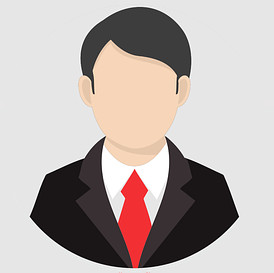
Mr.G. L.
-
Customer:
Confidential
-
Role:
Berater für Operations performance
-
Location:
Budapest
-
Turnover:
EUR 28 million (2017)
-
Time frame:
4 month
-
No. of employees:
140
About the Customer
The client is the Hungarian branch of the leading European provider of personalized digitally printed products like photobooks, greeting cards, calendars, wall decoration and other lifestyle products and serves customers in several countries in Europe, delivering either at home or to an affiliated retailer, where the customer will pick it up; the highly automated printing process must consider the uniqueness of each product ordered, as they are 100% customized. The client must hence strive to get the highest degree of automation while still producing in a 100% make-to-order mode. During Q4, a tenfold increase in orders is registered and 160 staff are employed at this production site, one of 10 for the head organization.
Testimonial from Сustomer
Mr. Z. Z., Managing Director: “The thorough investigation of our operations by Mr. G.L. revealed serious shortcomings in our processes. His analysis of the situation, his new strategy to reduce costs and optimize the production, and the solutions suggested all were so convincing, that we immediately invested in some equipment and began modifying the procurement processes, with expected purchasing savings of more than €40’000 in two months and 10-15% less working hours. Having had such a credible and effective professional on board, we are looking forward to a better performance.”
Situation (Challenge)
Running operations efficiently, especially the internal logistics, was difficult because the production site is spread over multiple stories, Goods reception, storage rooms and the various manufacturing areas all are on different floors, making the material flow very time-consuming. Insufficient storage space is also a burden for procurement. The client decided to get external help to optimize procurement and warehousing activities. The external consultant proposed to investigate the ordering and storage of raw materials, their internal distribution, and the impact of the facility’s layout on the internal logistics. The assignment lasted 2 months. After reception of the deliverables, the client suggested a second assignment regarding automation projects due to the excellent insights provided. Designing effective measures and innovative approaches to obtain greater efficiency required a RENT-A-MANAGER Executive with practical expertise and out-of-the-box thinking.
Solution (Achievement)
As well as introducing better forecasting and ordering algorithms for the procurement team, our RENT-A-MANAGER Executive prepared a six-month program to optimize and streamline the client’s warehousing activities. The cost of hiring the Executive was entirely self-liquidating. The project was completed on time and a significant reduction in direct and indirect costs, workload and complexity are expected after the implementation phase of the process modifications.